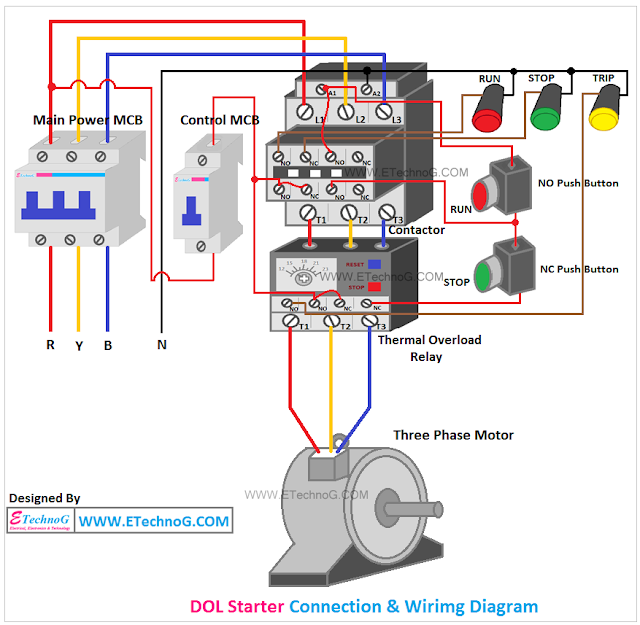
The gentle whir of a motor springing to life often goes unnoticed, a subtle soundtrack to our everyday routines. But behind that seamless start lies a crucial component: the electric motor starter relay. It’s the unsung hero, the silent facilitator of motion in countless applications, from household appliances to industrial machinery. But what exactly is this essential device, and why does it deserve our attention?
An electric motor starter relay acts as an intermediary between the power source and the motor, managing the high inrush current required during startup. Think of it as a gatekeeper, carefully orchestrating the flow of electricity to protect the motor from damage and ensure smooth operation. Without this critical device, motors could overheat, experience excessive wear and tear, or even fail completely.
The need for a device like the electric motor starter relay arose with the increasing use of electric motors in the late 19th and early 20th centuries. As motors grew larger and more powerful, the surge of current during startup became a significant concern. Early solutions were often cumbersome and inefficient, but the development of the electromagnetic relay paved the way for the modern, compact, and reliable starter relays we use today.
The evolution of the motor starting relay mirrors the progress of industrialization itself. From simple manual switches to sophisticated electronic controls, these devices have adapted to the demands of increasingly complex machinery and automation systems. Their importance cannot be overstated; they are the linchpin of modern manufacturing, transportation, and countless other industries that rely on electric motors.
The basic principle of an electric motor starter relay involves using a small control current to activate a larger circuit that handles the motor's starting current. This isolates the control circuit from the high-power motor circuit, ensuring safety and preventing damage to sensitive control components. A typical relay consists of an electromagnetic coil, a set of contacts, and a spring mechanism. When the control circuit energizes the coil, it creates a magnetic field that pulls the contacts together, closing the motor circuit and allowing current to flow to the motor.
Several benefits arise from using an electric motor starter relay. Firstly, it provides overload protection, preventing damage from excessive current. Secondly, it allows for remote control of the motor, eliminating the need for direct manual switching. Finally, using a relay simplifies the wiring and control circuitry, leading to more efficient and cost-effective systems. For instance, a simple push-button on a control panel can activate a large industrial motor miles away, thanks to the relay's ability to control high power with a low-power signal.
Troubleshooting electric motor starting relays often involves checking the coil for continuity, inspecting the contacts for wear or damage, and ensuring proper voltage at the control terminals. A multimeter is a valuable tool for diagnosing these issues. Common problems include burnt contacts, a faulty coil, or loose wiring connections.
Advantages and Disadvantages of Electric Motor Starter Relays
Advantages | Disadvantages |
---|---|
Overload protection | Potential relay failure |
Remote control capability | Can be affected by environmental factors (e.g., temperature, humidity) |
Simplified wiring and control | Requires periodic inspection and maintenance |
Best practices for implementing electric motor starter relays include selecting the appropriate relay for the motor's voltage and current requirements, ensuring proper wiring and grounding, and providing adequate ventilation to prevent overheating. Regular inspection and maintenance are also crucial for optimal performance and longevity.
Real-world examples of electric motor starter relays in action are abundant. They are found in HVAC systems, conveyor belts, pumps, compressors, and numerous other applications. For instance, in a refrigerator, the relay controls the compressor motor, starting and stopping it as needed to maintain the desired temperature.
Challenges related to electric motor starter relays can include contact wear, coil burnout, and sensitivity to environmental factors. Solutions often involve replacing worn components, ensuring proper ventilation, and using relays designed for specific operating conditions.
Frequently Asked Questions:
1. What is the function of an electric motor starter relay? (Answer: To control the high inrush current during motor startup.)
2. Why is overload protection important? (Answer: To prevent motor damage from excessive current.)
3. How does a relay work? (Answer: A small control current activates a larger circuit.)
4. What are common problems with relays? (Answer: Burnt contacts, faulty coil, loose wiring.)
5. How can I troubleshoot a relay? (Answer: Use a multimeter to check continuity and voltage.)
6. What are the benefits of using a relay? (Answer: Overload protection, remote control, simplified wiring.)
7. How do I choose the right relay? (Answer: Consider the motor's voltage and current requirements.)
8. What are some best practices for relay implementation? (Answer: Proper wiring, grounding, ventilation, regular maintenance.)
Tips and tricks for working with electric motor starter relays include using a wiring diagram to ensure proper connections, using the correct size wire for the current rating, and mounting the relay securely to prevent vibration and damage.
In conclusion, the electric motor starter relay, while often overlooked, plays a vital role in ensuring the efficient and safe operation of countless devices and systems that power our modern world. From the mundane hum of a refrigerator to the complex machinery of industrial plants, this unassuming component is essential for reliable motor control. Understanding its function, benefits, and proper implementation is key to maintaining productivity, minimizing downtime, and extending the lifespan of electric motors. By appreciating the intricacies of this small but mighty device, we can truly appreciate the sophisticated engineering that underpins our everyday lives. Take the time to understand the specific requirements of your application and choose the right relay for the job. Regular inspection and maintenance will also ensure long-term reliability and prevent costly downtime. Investing in quality relays and following best practices for implementation will pay dividends in the long run by ensuring smooth and efficient motor operation for years to come.
Stone spray paint near me revolutionizing diy stone decor
Bukit tunku houses your guide to prestigious kuala lumpur living
Cologne germany christmas market dates and festive delights